Differences Between 200, 300, 400, and 900 Series Stainless Steel
Feb 11,2025
The 200, 300, 400, and 900 series of stainless steel have distinct characteristics and applications based on their composition, performance, and cost. Let's examine the differences between these four families.
1. Corrosion Resistance
200 Series
Lower corrosion resistance compared to 300 series, especially in chloride-rich environments (e.g., seawater or acidic conditions).
Manganese and nitrogen help in certain applications, but overall corrosion resistance is not as high as 300 series.
300 Series
Exceptional corrosion resistance due to high nickel content and, in some alloys like 316, the addition of molybdenum for better protection against pitting and crevice corrosion.
Very good in chloride-containing environments and is the go-to choice for marine and food processing industries.
400 Series
Moderate corrosion resistance, lower than 300 series but better than plain carbon steel.
The martensitic steels (e.g., 410) are more susceptible to corrosion, especially in chloride-rich environments.
Ferritic steels (e.g., 430) are better than martensitic steels in corrosion resistance but still fall short compared to the 300 series.
900 Series
High corrosion resistance comparable to the 300 series, especially in alloys like 17-4 PH.
Designed for high-performance applications where corrosion resistance needs to be balanced with high strength.
Used in chemical, aerospace, and power generation industries, where extreme durability and corrosion resistance are required.
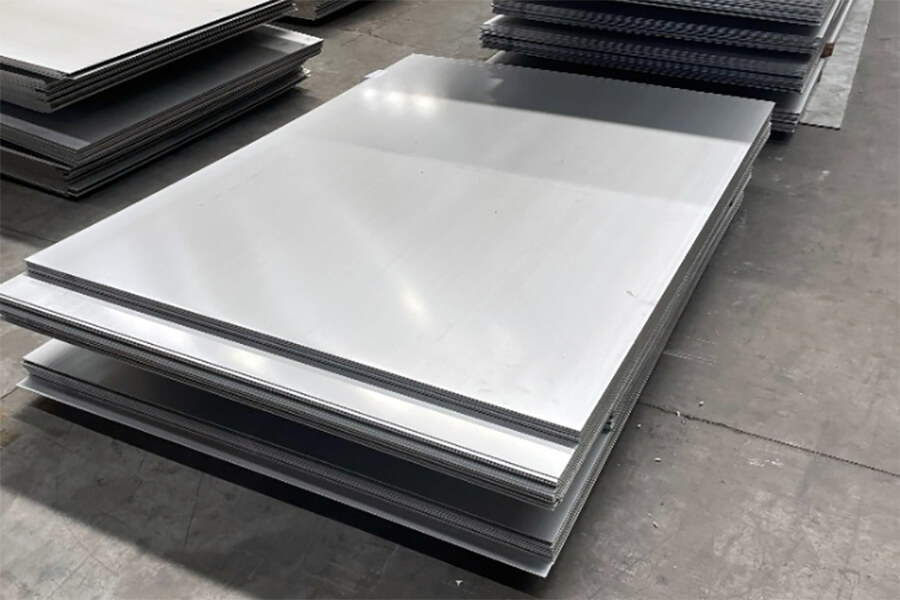
2. Applications
200 Series
Automotive components, kitchenware, appliances, structural components, and fasteners where high strength is needed but the exposure to corrosive environments is limited.
Decorative uses in situations that require strength at a lower cost.
300 Series
Food processing equipment, chemical processing, pharmaceutical equipment, medical devices, marine environments, and architectural applications.
304 is widely used in stainless steel countertops, equipment, and storage tanks for food and beverages.
316 is used for marine and chloride-rich environments.
400 Series
Automotive exhaust systems, heat exchangers, turbine blades, surgical tools, and appliances (especially 430).
410 and 420 are used in cutlery, tools, and industrial components that require high strength but not extreme corrosion resistance.
900 Series
Aerospace components, marine applications, chemical reactors, and other high-performance, high-strength environments.
17-4 PH and similar alloys are used for Turin critical, high-stress situations bine blades, valves, and pump parts in Sri
3. Cost
200 Series
Cheapest among the four, as the lower nickel content significantly reduces the production cost compared to 300 and 400 series.
Ideal for applications where cost savings are critical but high corrosion resistance isn’t the top priority.
300 Series
Expensive due to the high nickel and molybdenum content, but the higher cost is justified for corrosion-resistant applications like in the food industry, medical, chemical industries, and marine applications.
400 Series
Cheaper than the 300 series, but generally more expensive than the 200 series because of the chromium content.
Suitable for non-corrosive or mildly corrosive environments where cost savings are more important than extreme corrosion resistance.
900 Series
Most expensive due to the complex alloying and precipitation hardening process.
Used in high-performance applications where both strength and corrosion resistance need to be maximized, justifying the higher cost.
4. Magnetic Properties
200 Series
Magnetic after cold working because of the martensitic phase formed during processing.
Generally magnetic, unlike 300 series, which is usually non-magnetic.
300 Series
Non-magnetic in the annealed condition (with an FCC crystalline structure).
Can become slightly magnetic when cold-worked, but usually remains non-magnetic for most applications.
400 Series
Magnetic, as they include martensitic and ferritic steels, both of which have a body-centered cubic (BCC) structure that exhibits magnetic properties.
900 Series
Magnetic when cold worked, as the alloys often have a martensitic structure.
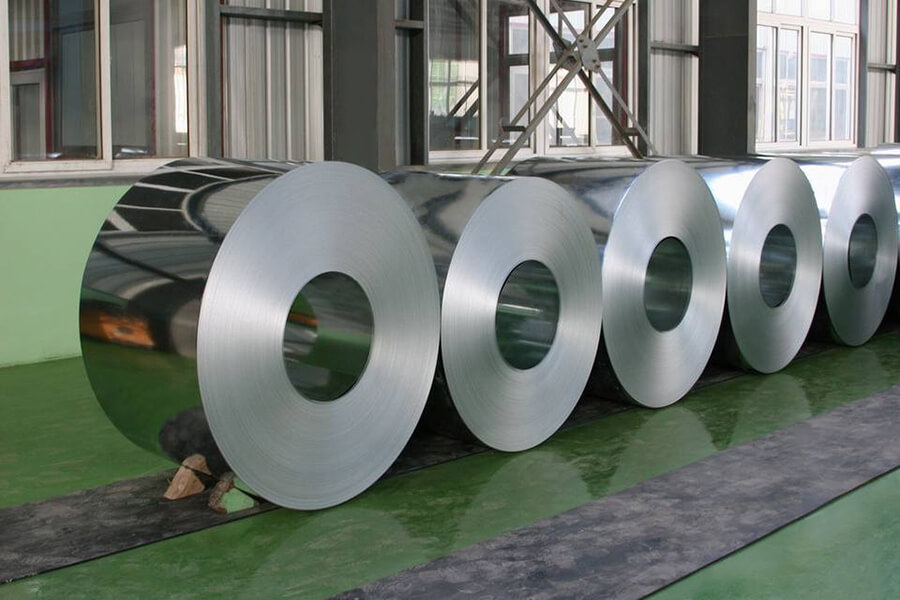
5. Strength and Toughness
200 Series
Higher tensile strength compared to 300 series, primarily due to the addition of manganese and nitrogen.
Generally, tougher than 300 series, making it suitable for structural applications, but less ductile than the 300 series.
300 Series
Lower tensile strength than the 200 series, but the ductility and weldability of the 300 series are much better.
The 300 series alloys are easier to form and weld, making them ideal for more complex shapes and parts that need to withstand cyclic stresses.
400 Series
Martensitic grades like 410 have higher strength but are less tough and more brittle compared to the 300 series.
Ferritic steels (e.g., 430) are less strong but are more ductile and resistant to brittle fracture.
900 Series
Very high strength due to precipitation hardening. These alloys are capable of achieving higher strength than typical 300 series alloys after heat treatment.
Often used in applications requiring both high strength and good corrosion resistance, such as in aerospace, oil and gas, and military applications.
6. Weldability
200 Series
Weldable, but due to their high tensile strength, weld cracking can be an issue in some grades, particularly for thicker sections. They often require special care during welding.
300 Series
Excellent weldability, which is one of the reasons they are widely used in welded structures and fabrications.
The 300 series alloys are designed to be easily welded without cracking.
400 Series
Weldability is good for ferritic steels like 430, but for martensitic grades (e.g., 410), they may require special procedures to avoid cracking during welding.
Martensitic steels can suffer from hardening and brittleness after welding.
900 Series
Can be welded, but the weldability is more challenging compared to 300 series stainless steels, primarily due to the need to maintain precise control over the heat treatment process.
Typically used in high-performance applications where welding is less common but may be required in certain conditions.
7. Composition
200 Series
Primary Alloying Elements: Manganese (Mn) and Nitrogen (N) substitute for nickel.
Chromium (Cr) content is 16-18% (similar to other stainless steels).
Nickel (Ni) content is lower (around 1-3%), which reduces the cost but impacts corrosion resistance.
300 Series
Primary Alloying Elements: Nickel (Ni) and Chromium (Cr) are the key alloying elements.
The most common grade is 304 (18% Cr, 8% Ni), but 316 (which includes 2-3% molybdenum) offers even better corrosion resistance.
Chromium is typically 16-20%.
The nickel content is around 8-10%.
400 Series
Primary Alloying Element: Chromium (Cr) is the main alloying element.
Nickel (Ni) is either absent or very low (<1%).
The chromium content typically ranges between 11-27% depending on the exact grade.
The 400 series is often magnetic and includes martensitic and ferritic stainless steels.
900 Series
Primary Alloying Elements: The 900 series includes specialized precipitation-hardening alloys like 17-4 PH, which contain elements like copper (Cu), niobium (Nb), and titanium (Ti) in addition to chromium and nickel.
These alloys can achieve very high strength through heat treatment (precipitation hardening).
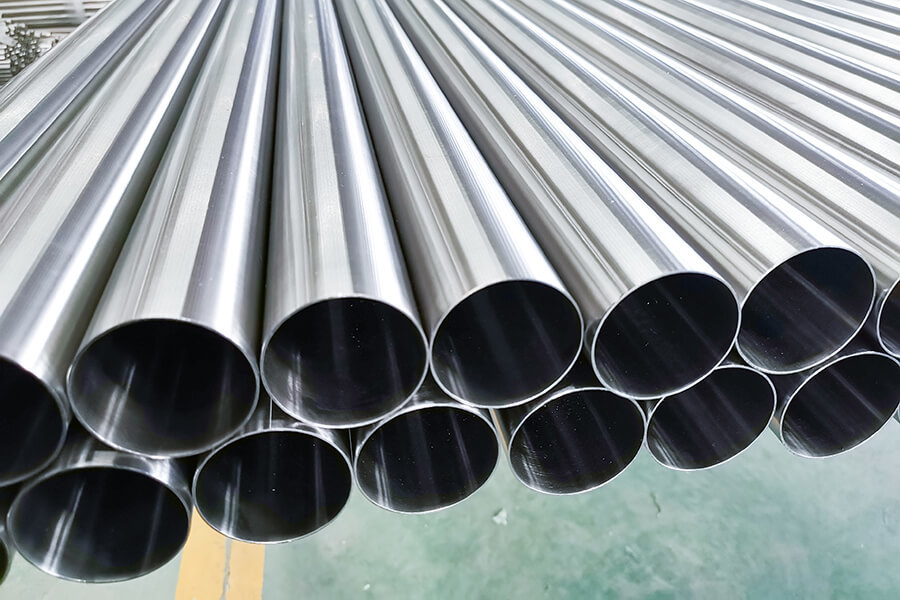
Summary
Series | Key Features | Corrosion Resistance | Strength | Magnetic | Cost | Applications |
200 | Manganese, Nitrogen, Lower Nickel | Lower, good for mild conditions | High | Magnetic | Low | Automotive, Appliances, Structural |
300 | High Nickel, Chromium | Excellent, for harsh conditions | Medium | Non-magnetic | High | Food, Medical, Chemical, Marine |
400 | Chromium (no nickel) | Moderate, for mild conditions | High | Magnetic | Medium | Automotive, Exhaust, Tools |
900 | Precipitation hardening alloys | High, for extreme conditions | Very High | Magnetic | Very High | Aerospace, Chemical, High-Performance |
Each series has unique attributes, making them suited for specific applications based on environmental exposure, strength requirements, and budget.
Next Page
Next page:
Latest News
Surface Selection of Stainless Steel
Jul 28,2025
Nickel Alloys: An In-Depth Overview
Feb 08,2025
View More