Know Stainless Steel Grades and Their Specific Applications
Jan 16,2025
As the most commonly used material in the world, stainless steels are classified into many types. Each type has different grades or alloys with varying chemical compositions and properties. Baoxing will introduce everything about stainless steel grades and their specific applications in this post. Now let’s dive into it.
Stainless Steel Types and Grades
1. Austenitic Stainless Steel
Grades: The most common grades of austenitic stainless steels are 200 and 300 series.
200 Series: Includes grades like 201 and 202, which have lower nickel content and are more cost-effective.
300 Series: Includes popular grades such as 304, 304L, 316, 316L, 321, 347, etc.
304: The most widely used, with good corrosion resistance.
316: Superior corrosion resistance, especially in chloride environments.
304L and 316L: Low carbon versions, ideal for welding.
Composition: Primarily made of iron, chromium (16-26%), nickel (6-22%), and small amounts of other elements like manganese and molybdenum.
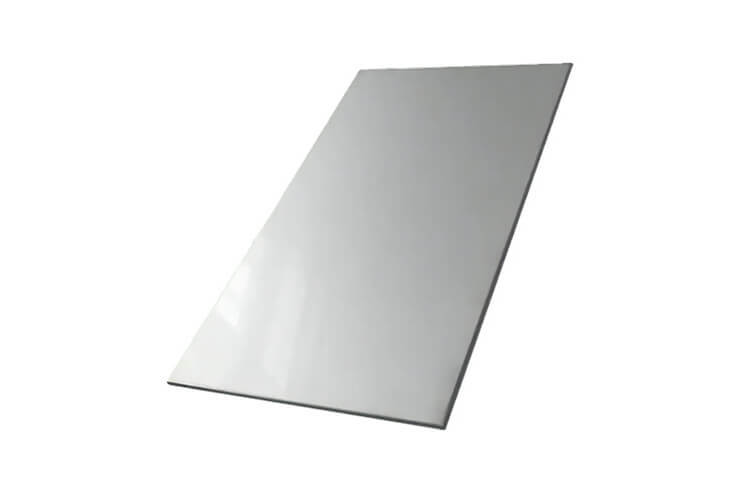
2. Ferritic Stainless Steel
Grades: Common grades include 400 Series.
409: Often used for automotive exhaust systems.
430: Commonly used for home appliances, kitchen utensils, etc.
441 and 444: These are higher-performing ferritic grades used in more aggressive environments.
Composition: Primarily contains chromium (10.5-30%), with low to no nickel content. It may also contain small amounts of molybdenum or other elements.
3. Martensitic Stainless Steel
Grades: Common grades are found in the 400 Series.
410: Common grade for cutlery, valves, and pumps.
420: Often used in knives and surgical instruments due to its hardness after heat treatment.
440A, 440B, 440C: High-carbon versions that offer high hardness and wear resistance.
Composition: These steels typically have a higher carbon content (0.08% to 1.2%) and around 12-18% chromium. The higher carbon content allows for greater hardness but less corrosion resistance.
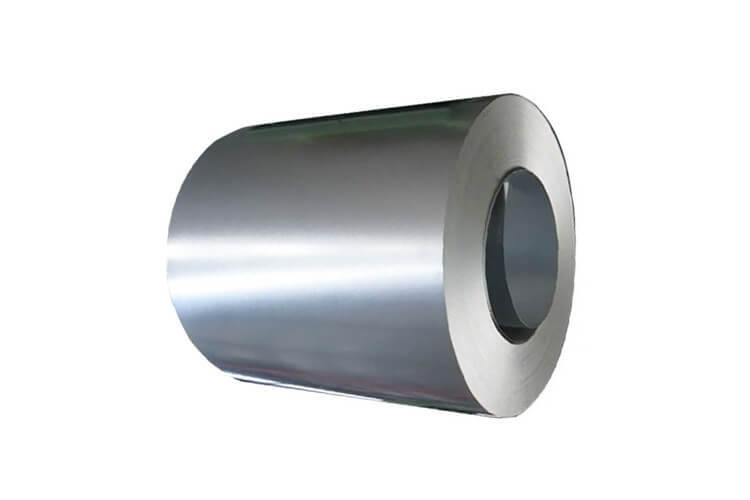
4. Duplex Stainless Steel
Grades: Duplex stainless steels have a mix of austenitic and ferritic microstructures, providing high strength and excellent corrosion resistance.
2205: One of the most common duplex grades used in applications requiring high resistance to pitting and crevice corrosion.
2507: Super duplex stainless steel, known for its superior corrosion resistance, especially in chloride-rich environments.
Composition: These steels typically contain around 22-25% chromium, 4-7% nickel, and 3% molybdenum, with nitrogen added to improve strength and resistance to stress corrosion cracking.
Summary of Grades:
Austenitic: 200 Series (e.g., 201, 202), 300 Series (e.g., 304, 316)
Ferritic: 400 Series (e.g., 409, 430)
Martensitic: 400 Series (e.g., 410, 420, 440)
Duplex: 2205, 2507
Specific Applications of Each Grade of Stainless Steel
Various stainless steel grades are used across a wide range of industries, each with unique properties. Here's an overview of the main applications and industries where each grade is typically used.
1. Austenitic Stainless Steel (200 and 300 Series)
Key Properties: High corrosion resistance, good formability, excellent weldability, non-magnetic, and good strength at elevated temperatures.
Common Grades: 201, 202, 304, 304L, 316, 316L, 321, 347
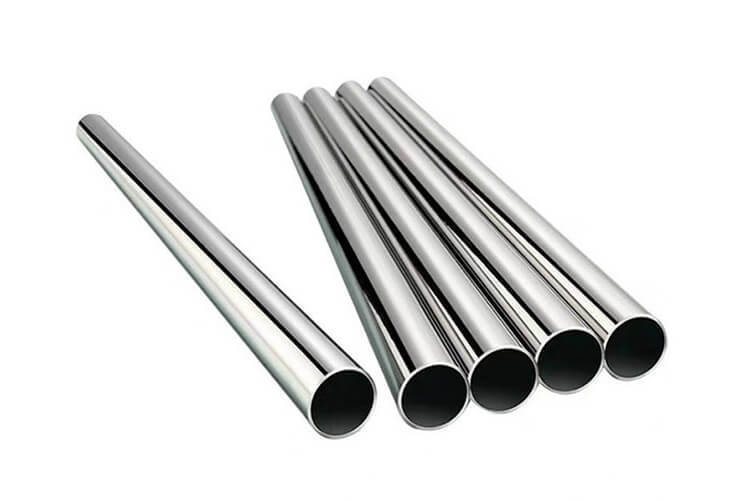
Main Industries & Applications:
Food and Beverage: 304 and 316 are widely used for food processing equipment, dairy equipment, and kitchen appliances due to their excellent corrosion resistance.
Chemical and Petrochemical: 316 and 316L are used for reactors, heat exchangers, and tanks due to their resistance to acidic environments.
Pharmaceutical: 316L is frequently used for pharmaceutical equipment such as mixers and storage tanks, where hygiene is paramount.
Marine: 316 is preferred for marine applications (shipbuilding, offshore platforms) due to its superior resistance to corrosion in saline environments.
Medical: 316L is used in surgical instruments, implants, and hospital equipment due to its biocompatibility and resistance to corrosion.
Construction: Architectural components, facades, and railings made from 304 or 316 due to their aesthetic appearance and durability.
Aerospace: 304 and 321 are used in components like fuel tanks, engine parts, and airframe structures due to their strength and resistance to high temperatures.
Automotive: 304 and 316 are used for exhaust systems, catalytic converters, and other components exposed to high temperatures and corrosive environments.
2. Ferritic Stainless Steel (400 Series)
Key Properties: Good corrosion resistance in mild environments, magnetic, better resistance to stress corrosion cracking, and cost-effective.
Common Grades: 409, 430, 441, 444
Main Industries & Applications:
Automotive: 409 and 430 are commonly used for exhaust systems, mufflers, catalytic converters, and other under-the-hood components due to their high resistance to corrosion in exhaust gas environments.
Home Appliances: 430 is widely used in kitchen appliances like refrigerators, dishwashers, and ovens because of its good corrosion resistance and formability.
Architecture: Ferritic stainless steels are used in architectural panels, decorative trims, and roofing due to their aesthetic appeal and good weather resistance.
Industrial Equipment: 430 is used for heat exchangers, pressure vessels, and other industrial applications where moderate corrosion resistance is required.
Food Industry: 430 is used in some food processing equipment, particularly where the surface finish is a key requirement, like cooking surfaces and storage containers.
3. Martensitic Stainless Steel (400 Series)
Key Properties: High hardness, wear resistance, and strength, but less corrosion resistance compared to austenitic and ferritic grades. Can be heat-treated to achieve a range of properties.
Common Grades: 410, 420, 440A, 440B, 440C
Main Industries & Applications:
Cutlery: 420 and 440 grades are commonly used for knives, scissors, and other cutlery due to their ability to take a sharp edge after heat treatment.
Surgical Instruments: 420 and 440C are used in medical devices such as scalpels, forceps, and surgical blades because of their strength and sharpness.
Pumps and Valves: 410 and 420 are used in pumps, valves, and other equipment that require both strength and corrosion resistance in low-corrosive environments.
Tooling: 440C is used in tooling applications, such as ball bearings, gears, and die inserts, because of its hardness and wear resistance.
Industrial Equipment: Martensitic grades are used in machinery components, like shafts and gears, where high strength and resistance to wear are required.
4. Duplex Stainless Steel
Key Properties: High strength, excellent resistance to pitting, crevice corrosion, and stress corrosion cracking, and good weldability. It combines the properties of both austenitic and ferritic steels.
Common Grades: 2205, 2507 (Super Duplex)
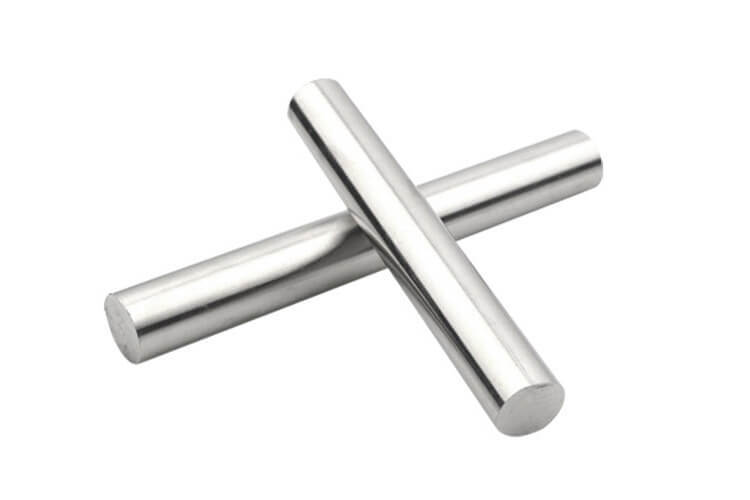
Main Industries & Applications:
Oil and Gas: Duplex stainless steels are commonly used in oil and gas pipelines, offshore platforms, and refineries due to their excellent resistance to corrosion in saline and harsh environments.
Chemical Processing: 2205 and 2507 are used for chemical reactors, heat exchangers, and storage tanks, especially where corrosion resistance to chlorides and acids is important.
Marine: 2205 and 2507 are ideal for marine applications such as seawater piping, desalination plants, and offshore structures, due to their ability to withstand chloride stress corrosion cracking.
Power Generation: These steels are used in power plants, especially in heat exchangers and cooling systems that are exposed to high-stress corrosion environments.
Pulp and Paper: 2205 is often used for pulp and paper mill equipment where chloride stress corrosion resistance is critical.
Desalination: 2205 is commonly used in desalination plants for components exposed to seawater due to its excellent resistance to seawater corrosion.
Summary of Key Applications by Grade
Austenitic (300 Series): Food processing, chemical & pharmaceutical, medical devices, aerospace, marine, construction, automotive.
Ferritic (400 Series): Automotive exhaust, home appliances, architecture, industrial equipment, food industry.
Martensitic (400 Series): Cutlery, surgical instruments, tooling, industrial equipment, valves & pumps.
Duplex: Oil & gas, chemical processing, marine, pulp & paper, desalination, power generation.
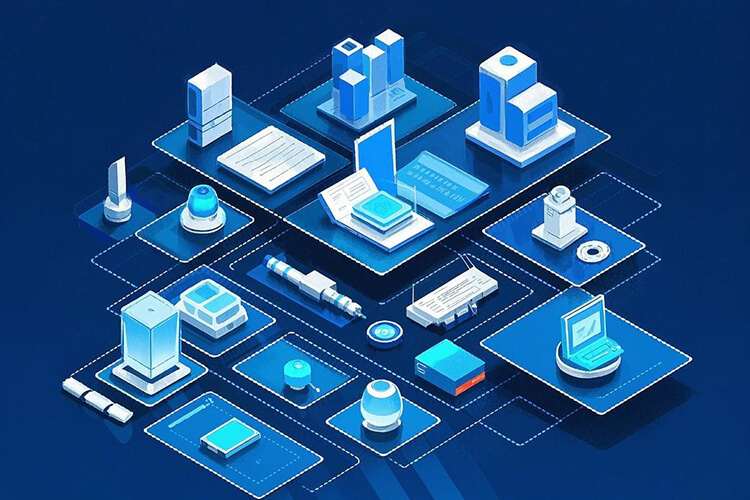
How to Choose the Proper Stainless Steel Grade?
Selecting the right grade of stainless steel for a particular application requires careful consideration of several key factors, including corrosion resistance, mechanical properties, environmental conditions, fabrication requirements, and cost. Here’s a step-by-step guide to help you select the most suitable stainless steel grade.
1. Determine the Corrosion Environment
Corrosive Conditions: If the application will be exposed to chemicals, salt water, or acidic/alkaline conditions, you need a stainless steel that offers high corrosion resistance.
For mild environments, grades like 304 (austenitic) or 430 (ferritic) might be sufficient.
For highly corrosive environments, such as exposure to chloride-rich environments (seawater or chemicals), grades like 316 (austenitic) or 2205 (duplex) offer better resistance to pitting and stress corrosion cracking.
Highly acidic environments (e.g., sulfuric acid) may require specialized alloys such as 904L or Super Duplex (2507).
2. Consider Strength and Hardness Requirements
If the application involves high mechanical stress (e.g., high pressure or wear conditions), you’ll need a grade that offers sufficient strength and hardness.
Martensitic stainless steels (e.g., 410, 420, 440C) are ideal for applications requiring high hardness and wear resistance, such as cutlery, surgical instruments, and tools.
Duplex stainless steels (e.g., 2205, 2507) are also good choices for applications requiring both strength and corrosion resistance, such as oil & gas pipelines and marine structures.
3. Evaluate Temperature and Environmental Conditions
High-Temperature Resistance: If the application involves high temperatures (e.g., furnace parts, exhaust systems, or turbines), consider grades that maintain strength and oxidation resistance at elevated temperatures.
Grade 304 is commonly used in high-temperature environments, but if higher heat resistance is needed, 321 or 347 (austenitic) may be more appropriate due to their better performance in heat-resistant environments.
For cryogenic conditions, austenitic stainless steels (e.g., 304, 316) perform well because they remain tough and resistant to brittle fracture at low temperatures.
4. Consider Fabrication and Welding Requirements
Ease of Forming and Welding: If the component needs to be formed or welded, you should consider how easily the grade can be worked with and whether the final product needs to meet certain weldability criteria.
Austenitic stainless steels (e.g., 304, 316, 321) are known for their excellent weldability and formability.
For applications requiring heavy welding, grades like 304L and 316L (low-carbon versions) reduce the risk of carbide precipitation and ensure better weld quality.
Ferritic stainless steels (e.g., 430, 409) have lower weldability but can be more cost-effective for less demanding applications.
5. Determine the Aesthetic and Surface Finish Needs
For applications requiring a polished or decorative finish, such as architectural components, kitchen appliances, or consumer goods, you’ll need a stainless steel that can achieve a smooth, attractive surface.
Austenitic stainless steels like 304 and 316 can achieve high-quality finishes.
Ferritic and martensitic stainless steels generally don't offer the same level of aesthetic appeal as austenitic grades but can still be used in architectural applications with less demanding finish requirements.
6. Consider Mechanical Property Requirements
Ductility and Toughness: If the application involves parts that will undergo forming, stretching, or bending, you'll need ductile and stainless steel.
Austenitic stainless steels (e.g., 304, 316) are typically more ductile and can be easily formed into complex shapes.
Impact Toughness: A tough and impact-resistant material is essential for components that will be exposed to impacts or vibrations (e.g., automotive or marine applications).
Duplex stainless steels (e.g., 2205) are both strong and tough, making them suitable for high-impact environments.
7. Assess Cost Considerations
Stainless steels vary in cost, with some grades being more expensive than others due to their alloy content (e.g., high nickel content in austenitic grades).
Ferritic stainless steels like 430 or 409 are usually more cost-effective and can be used in less demanding applications.
Austenitic grades like 304 and 316 are more expensive due to the higher nickel content, but they offer better corrosion resistance and mechanical properties.
Duplex grades (e.g., 2205) are typically more expensive but offer a good balance of strength and corrosion resistance, which may justify the cost in certain high-performance applications.
8. Industry-Specific Standards and Regulations
Certain industries may have specific standards, certifications, or regulations that govern material selection. For example:
Food and medical industries often require 316L (low-carbon) for hygiene and resistance to bacterial growth.
Automotive and aerospace industries might prefer grades with specific mechanical properties, heat resistance, or low weight.
Practical Example of Choosing a Grade
Food processing equipment: The material must resist acidic foods and cleaning chemicals while being easy to clean. 304 or 316 would be ideal because they provide excellent resistance to a wide range of food acids and can be polished to a smooth finish for hygiene purposes.
Automotive exhaust system: A material that can withstand high temperatures and corrosive exhaust gases. 409 or 430 are commonly used for exhaust systems as they offer good resistance to oxidation at high temperatures.
Cutlery and surgical instruments: 420 or 440C for their ability to hold a sharp edge and resist wear. 440C is often used for high-end knives because of its hardness after heat treatment.
Summary of Key Considerations
Corrosion Resistance: Consider the specific chemicals, salts, and environments the material will be exposed to.
Strength and Hardness: Assess mechanical loading, wear resistance, and hardness requirements.
Temperature: Determine if the material needs to withstand high or low temperatures.
Fabrication: Consider how easy the material is to form, weld, and machine.
Cost: Balance performance needs with budget constraints.
Industry Standards: Ensure compliance with any specific industry regulations or standards.
Summary
By knowing the classifications, grades, and applications of stainless steel, you can choose the appropriate grade of stainless steel that meets your needs in terms of performance and cost. If you still need help, please do not hesitate to contact us.
Previous Page:
Latest News
Surface Selection of Stainless Steel
Jul 28,2025
Nickel Alloys: An In-Depth Overview
Feb 08,2025
View More