Galvanized Steel Types, Features, and Applications
Jan 14,2025
Galvanized steel refers to steel coated with a layer of zinc through various methods to prevent rust and corrosion. Zinc acts as a protective shield for steel, allowing it to withstand harsh environments while maintaining its strength. Galvanization also extends the lifespan of steel, making it ideal for outdoor, industrial, and marine applications.
What Is Galvanization?
Galvanization is applying a protective zinc coating to steel or iron to prevent rusting and corrosion. The primary purpose of galvanization is to enhance the durability and longevity of steel or iron by protecting it from the elements, such as moisture, oxygen, and salts, which are the main causes of corrosion.
The basic mechanism behind galvanization is that zinc forms a protective barrier when applied to steel. Zinc is more reactive than steel, so it corrodes first (a process called sacrificial protection) and acts as a protective shield for the underlying metal. This means that even if the coating gets scratched or damaged, the exposed steel is still protected by the surrounding zinc that continues to corrode instead of the steel.
Types of Galvanized Steel
1. Hot-dip galvanized Steel
Process: This is the most common and traditional method of galvanizing. The steel is cleaned to remove any contaminants (oil, grease, rust) and then dipped into a bath of molten zinc at around 450°C (840°F). The zinc forms a metallurgical bond with the steel, creating a durable, corrosion-resistant coating.
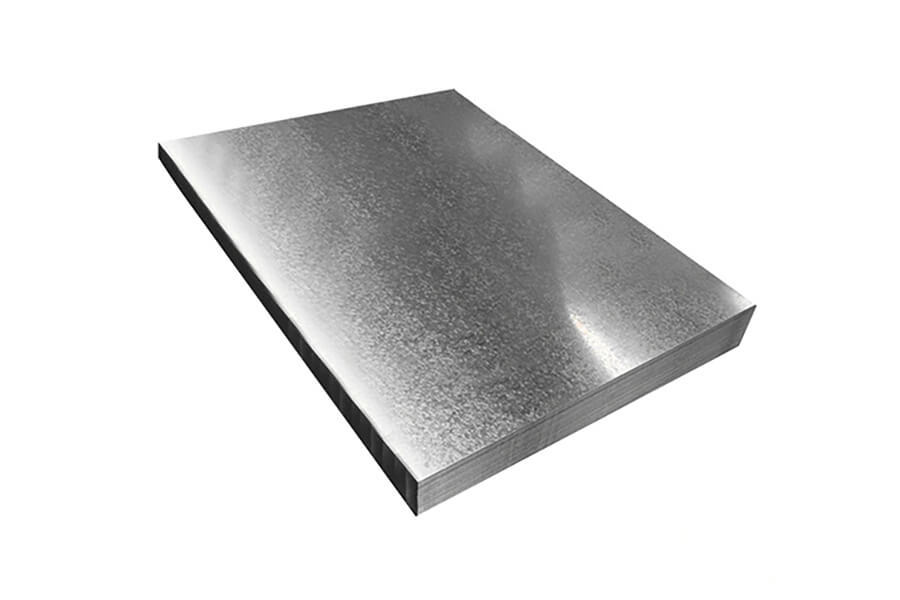
Features
Thick Coating: The zinc coating is thicker compared to other methods, providing long-lasting protection.
Rougher Surface: The coating has a matte finish with a crystalline structure that can vary in appearance depending on the cooling rate.
Long-Term Protection: High corrosion resistance, typically lasting 20-50 years depending on the environmental conditions.
Sacrificial Anode: The zinc corrodes first, protecting the underlying steel from corrosion.
Applications
Construction: Used in structural steel, framing, and reinforcements in buildings and infrastructure.
Fencing and Barriers: Popular for fencing systems, gates, and temporary barriers.
Roofing and Gutters: Offers long-term weather resistance in roofing panels, downspouts, and gutters.
Agriculture: Used for silos, agricultural sheds, and animal enclosures due to its ability to resist harsh weather and humidity.
2. Electro-Galvanized Steel
Process: This method involves electroplating, where steel is immersed in an electrolyte bath containing zinc salts. An electric current is passed through the bath, causing the zinc to bond with the steel surface. The coating is much thinner than hot-dip galvanization.
Features
Smooth Finish: The electroplating process results in a smooth, even surface, which makes it suitable for applications requiring aesthetic appeal.
Thinner Coating: Typically provides a thinner, more uniform coating than hot-dip, offering less corrosion resistance but still effective in mild environments.
Less Sacrificial Protection: Due to the thinner zinc layer, it provides less long-term sacrificial protection.
Cost-Effective: Generally less expensive than hot-dip galvanizing, though it may not be suitable for high-corrosion environments.
Applications
Automotive Parts: Electro-galvanized steel is used for car body parts that are protected from mild rusting but do not face extreme conditions.
Home Appliances: Found in items such as washers, dryers, refrigerators, and other small appliances.
Electronics: Common in enclosures, panels, and housings where a smooth finish is needed.
Interior Components: Often used in applications where the steel is not exposed to severe weather.
3. Galvannealed Steel
Process: After hot-dip galvanizing, the coated steel is further heated to allow the zinc to alloy with the steel, forming a unique zinc-iron coating that is more durable and has superior paint adhesion qualities. The process gives the steel a smooth, matte finish.
Features
Superior Paintability: The alloyed surface promotes excellent adhesion of paints, making it ideal for applications that require a painted finish.
Improved Formability: Galvannealed steel is more formable than hot-dip galvanized steel, meaning it can be easily shaped without cracking the coating.
Enhanced Weldability: Unlike traditional galvanized steel, which can produce hazardous fumes when welded, galvannealed steel is safer to weld and is often used in applications where welding is required.
Applications
Automotive Industry: Often used for outer body panels, such as hoods, doors, and fenders, where corrosion resistance and paint adhesion are essential.
Appliance Industry: Popular in appliances that require high-quality paint finishes, such as refrigerators and washers.
Electronics: Ideal for high-quality, durable casings or enclosures that need a smooth finish for both aesthetic and functional purposes.
4. Pre-Galvanized Steel
Process: In this method, steel is coated with zinc before being formed into the final shape (e.g., coils, sheets, or strips). The steel passes through a molten zinc bath during the manufacturing process, and the coating is applied before the material is stamped or rolled into products.
Features
Inconsistent Coating: The zinc coating may be thinner in areas where the material is bent or shaped after galvanization.
No Post-Processing: Pre-galvanized steel is often used where no further surface treatment is required after the product is made.
Moderate Corrosion Resistance: The coating provides good resistance to rust and corrosion, but less so than hot-dip galvanization.
Applications
Roofing and Cladding: Used in the construction of roofing sheets and wall cladding where moderate protection is sufficient.
HVAC Systems: Often used for ductwork, air handling units, and other HVAC components that are exposed to mild environmental conditions.
Light Structural Components: Ideal for non-load-bearing applications where moderate protection against rust is needed.
Features of Galvanized Steel
Corrosion Resistance
The zinc coating prevents steel's direct exposure to environmental elements like water, oxygen, and salts. Zinc corrodes slowly, protecting the steel underneath. In hot-dip galvanization, the zinc forms a stable, non-reactive layer that is highly resistant to rust.
Durability and Longevity
Galvanized steel can withstand years of exposure to the elements. The thickness of the coating determines its lifespan. Hot-dip galvanized steel can last 20-50 years in most outdoor environments.
Cost-Effectiveness
Galvanized steel is often chosen for its cost-effectiveness, especially when compared to stainless steel or other corrosion-resistant materials. Its relatively low cost and long lifespan make it a popular choice for a wide range of industries.
Aesthetic Flexibility
Galvanized steel can be painted, allowing for additional customization in appearance. It’s available in a variety of finishes from smooth to textured, providing versatility for both functional and decorative uses.
Environmental Resistance
Galvanized steel is highly resistant to extreme weather conditions, including high humidity, acid rain, and seawater, making it suitable for marine, agricultural, and industrial environments.
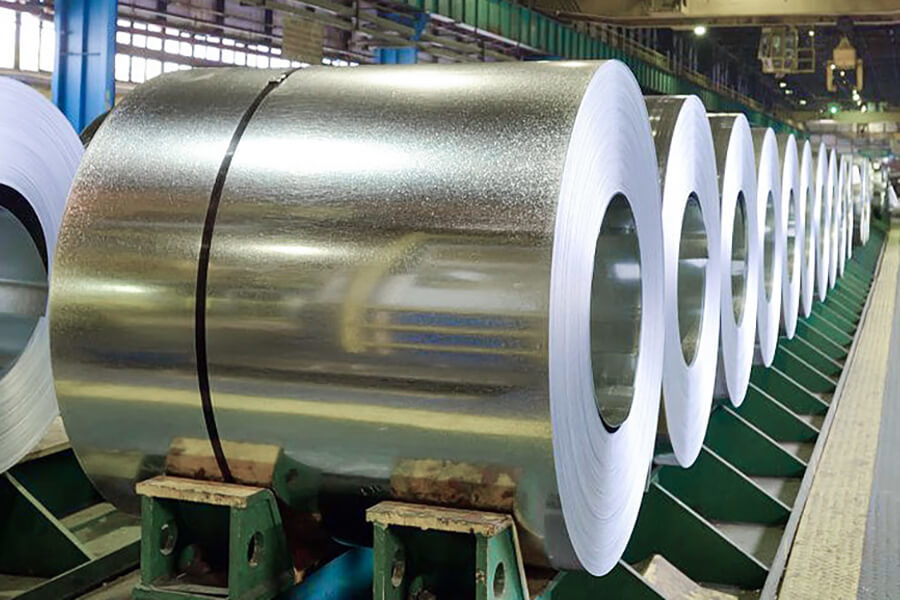
Applications of Galvanized Steel
Construction
Structural Support: Galvanized steel is used in load-bearing applications such as columns, beams, and trusses due to its ability to withstand harsh outdoor conditions.
Infrastructure: Bridges, tunnels, and communication towers are often made from galvanized steel to ensure longevity and durability in exposed environments.
Building Materials: Common in the fabrication of roofing, cladding, gutters, and downspouts where corrosion resistance is crucial.
Automotive
Vehicle Frames and Components: Automakers use galvanized steel for parts that are exposed to environmental stress, such as chassis, bumpers, and underbody panels.
Corrosion Protection: The automotive industry widely uses galvanized steel for rust protection, especially in undercoating to protect against road salt and moisture.
Agriculture
Farm Structures: Galvanized steel is used for greenhouses, storage buildings, silos, and livestock pens due to its resistance to moisture and humidity.
Fencing: Galvanized wire is commonly used for fencing, gates, and animal enclosures where rust resistance is essential for safety and longevity.
Industrial and Heavy-Duty Applications
Piping: Galvanized steel pipes are used for water distribution, gas lines, and industrial applications where moisture and chemicals may cause steel to corrode.
Electrical Equipment: Electrical towers, poles, and enclosures for equipment are often made from galvanized steel to withstand environmental factors.
Home Appliances
Washing Machines and Refrigerators: These products benefit from galvanized steel's resistance to moisture and ease of cleaning.
HVAC Systems: Galvanized steel is widely used for ductwork and air conditioning systems, ensuring durability in both residential and commercial settings.
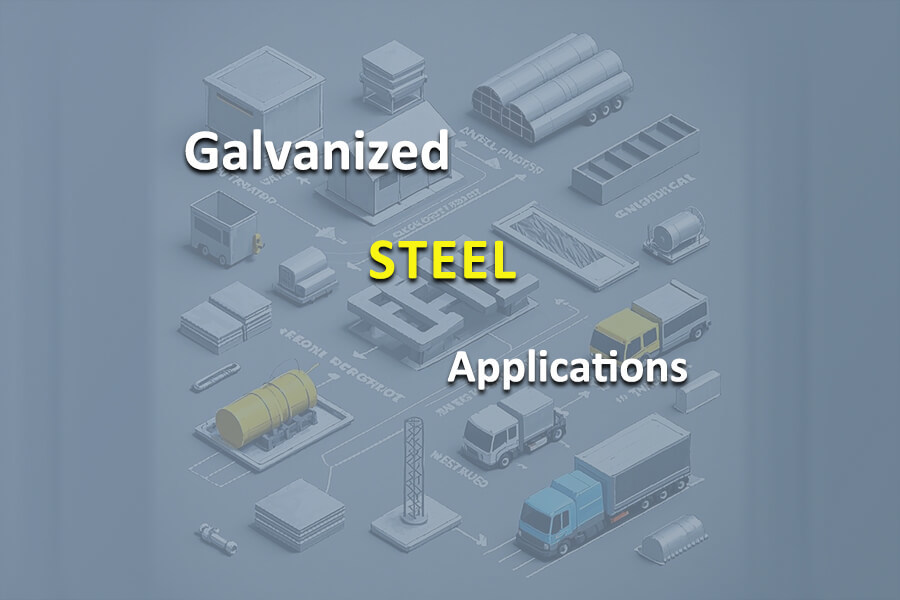
Advantages of Galvanized Steel
Long-Term Protection: Galvanized steel is known for its long lifespan, often providing 20 to 50 years of protection depending on the coating thickness and environment.
Minimal Maintenance: Once galvanized steel is installed, it requires very little maintenance or treatment.
Economic Choice: Compared to stainless steel, galvanized steel is a more affordable solution with comparable rust protection in most applications.
Wide Availability: Galvanized steel is easily accessible across industries, making it an ideal choice for a wide range of projects.
Conclusion
If you're choosing galvanized steel for a specific application, the right type depends on factors like environmental exposure, required durability, and cost. Or, you can contact us to get a professional solution for your project.
Latest News
Surface Selection of Stainless Steel
Jul 28,2025
Nickel Alloys: An In-Depth Overview
Feb 08,2025
View More